Bosch Diesel Service / Bosch Diesel Center
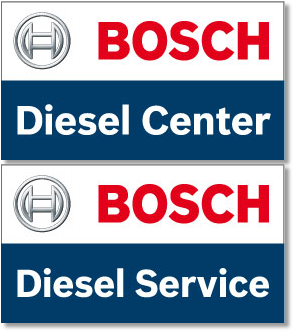
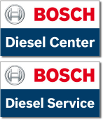
Wymieniać potrafi każdy, naprawiać tylko eksperci
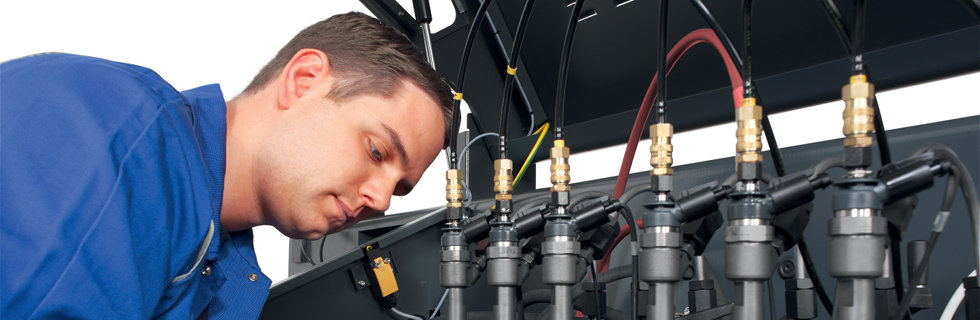
Rozszerzona technologia napraw pompowtryskiwaczy UIP do samochodów osobowych grupy VW
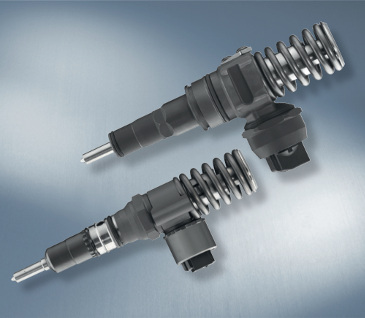
VW TDI z pompowtryskiwaczami nadal budzi szacunek. Systemy zasilania silników diesla w samochodach osobowych z pompowtryskiwaczami były powszechnie stosowane w markach koncernu VW od 1997 roku.
Stosowano dwa główne rodzaje pompowtryskiwaczy – pierwszej generacji UIP1.x do silników z dwoma oraz drugiej generacji UIP2.0 do silników z czterema zaworami na cylinder. W pierwszej generacji występuje jeszcze kilka podtypów różniących się częściowo budową wewnętrzną.
Od roku 2009 zaczęto je sukcesywnie zastępować układem Common Rail, a w roku 2012 zaprzestano ich produkcji i stosowania w samochodach europejskich. Wycofanie wynikało z konieczności wprowadzenia więcej niż dwóch faz wtrysku, tak by dostosować układ wtryskowy do wymagań kolejnych norm spalin. Systemy CR pod wieloma względami bardziej się do tego nadają.
Niemniej jednak pojazdy z pompowtryskiwaczami są wciąż powszechnie użytkowane w krajach europejskich. Oznaczenie TDI nadal budzi szacunek. Szczególnie chętnie ze względu na dużą niezawodność importowane są do krajów Europy Wschodniej w tym również do Polski.
Obecnie auta te znajdują się w „szczytowym momencie” napraw z uwagi na fakt, że najwięcej produkowano ich w latach 2002-2008, co oznacza, że mają już około 8-14 lat.
I i II etap naprawy
Około roku 2007 firma Bosch wprowadziła I oraz II etap napraw tych elementów wtryskowych.
Naprawa obejmowała głównie:
- wymianę zestawu końcówki wtrysku wraz z nakrętką oraz uszczelnień zewnętrznych
- regulację ciśnienia otwarcia końcówki wtrysku (rozpylacza)
- testowanie na stanowisku EPS 815 z wyposażeniem Cam Box
W owym czasie taki poziom naprawy był wystarczający, ponieważ przebiegi kilometrowe samochodów wyposażonychw ww. układy nie powodowały w większości rozregulowania lub zużycia elektromagnetycznego zaworu sterującego. Zużyciu ulegały głównie końcówki wtrysku, podlegające obciążeniom termicznym oraz uszczelnienia w głowicy silnika.
Obecnie przebiegi tych aut są znacznie większe, więc często wymiana elementów dolnej części pompowtryskiwacza i uszczelnień nie gwarantuje prawidłowej pracy. Przyczyną tego może być nieprawidłowy początek wtrysku tzw. BIP-u, którego wartość zależy od prawidłowych skoków iglicy, nacisków sprężyn i sprawności elektromagnesu sterującego.
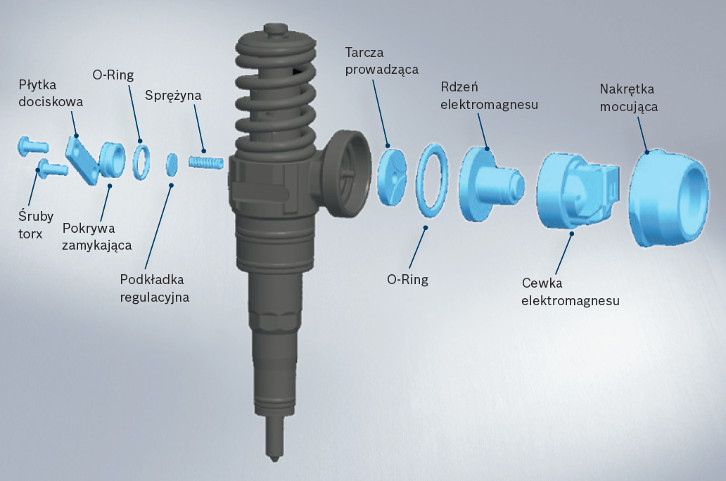
Rys. 1 Budowa zespołu elektromagnetycznego zaworu sterującego UIP
BIP – faktyczny początek wtrysku
Jednym z najważniejszych parametrów pracy pompowtryskiwacza jest właśnie BIP (Begin of Injection Period), będący faktycznym początkiem wtrysku.
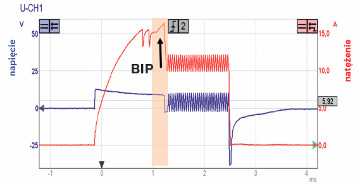
Rys. 2 Wykres prądu i napięcia w czasie, prezentujący BIP
Powyższy wykres przedstawia przebieg napięcia oraz prądu sterującego pracą pompowtryskiwacza w czasie, na którym BIP został wskazany strzałką. Wspomniany BIP powinien mieścić się w granicach tolerancji określonej przez producenta. Na podstawie tej wartości odniesionej do sygnałów z czujników obrotów wału korbowego oraz czujnika Halla na wałku rozrządu, sterownik silnika steruje podstawowym parametrem jego pracy czyli przebiegiem zapłonu w stosunku do GMP oraz czasem wtrysku czyli dawką.
Z czasem, z powodu milionów cykli pracy wykonanych przez pompowtryskiwacz, obniża się sprawność elementów mechanicznych zaworu sterującego czyli: pasowanie iglicy sterującej w korpusie, szczelność przylgni gniazda, wielkość skoku iglicy oraz napięcie sprężyny cofającej. Uszkodzenia przekładają się na opóźnienie wtrysku oraz niepełne dawki wtryskiwanego paliwa, co objawia się zazwyczaj obniżeniem mocy silnika, nierówną pracą, dymieniem i zawyżonym zużyciem paliwa.
III etap naprawy
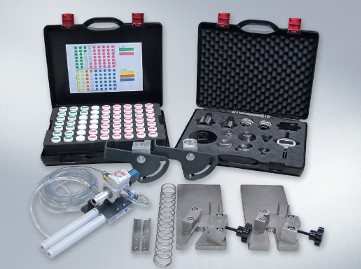
Rys. 3 Kompletny zestaw narzędzi III etapu
napraw pompowtryskiwaczy
W roku 2016 firma Bosch rozszerzyła technologię regeneracji pompowtryskiwaczy, którą nazwano „trzecim etapem naprawy”. Jak zwykle postawiono na profesjonalizm pozwalający wykonać skuteczną naprawę wysokiej jakości w odniesieniu do realnej wartości samochodu.
Opracowano specjalistyczne narzędzia umożliwiające wykonanie precyzyjnych pomiarów i regulacji poszczególnych części oraz parametrów funkcjonalnych w obszarze zaworu sterującego. Wielkości te mierzy się i ustawia z mikronową dokładnością.
Nowy etap naprawy polega głównie na przywróceniu właściwej kinematyki i dynamiki pracy zaworu poprzez wyregulowanie właściwego skoku iglicy sterującej oraz napięcia sprężyny cofającej. Regulację skoku wykonujemy poprzez wymianę tarczy prowadzącej, znajdującej się między tłoczkiem uszczelniającym a elektromagnesem, natomiast napięcie sprężyny poprzez podkładkę regulacyjną umieszczoną nad sprężyną. Dzięki takim ustawieniom uzyskujemy prawidłowy BIP podczas pracy silnika, który po naprawie należy sprawdzić podczas testu na stole probierczym.
Aby umożliwić precyzyjne pomiary trzeciego etapu naprawy w zestawie znalazły się (Rys. 3):
- precyzyjny cyfrowy miernik „zegarowy” (Rys. 4)
- urządzenie do sprawdzania szczelności pompowtryskiwacza (Rys. 5)
- narzędzia kalibracyjno-pomiarowe
- wyposażenie do imadła montażowego umożliwiające zamocowanie pompowtryskiwaczy podczas wykonywania czynności naprawczych
- walizka z podkładkami regulacyjnymi
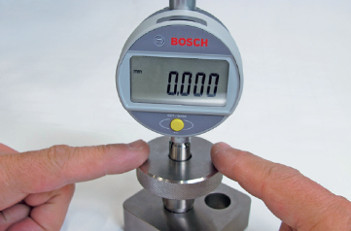
Rys. 4 Precyzyjny wysokościomierz cyfrowy
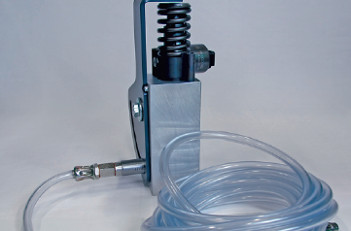
Rys. 5 Urządzenie do testowania szczelności
Przebieg naprawy
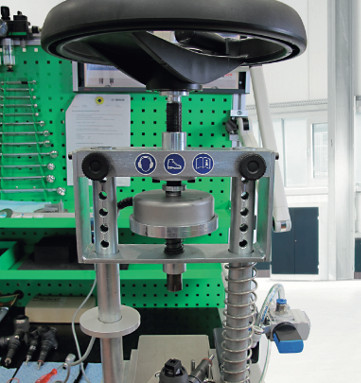
Rys. 6 Demontaż pompowtryskiwacza w imadle naprawczym
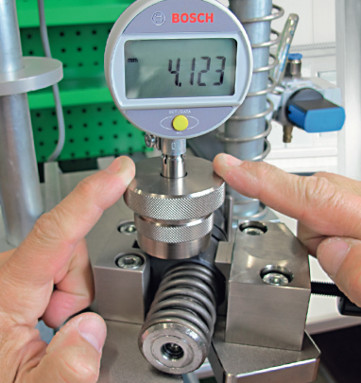
Rys. 7 Pomiar cyfrowym miernikiem
Przed przystąpieniem do naprawy należy sprawdzić działanie pompowtryskiwacza na stanowisku diagnostycznym EPS 815 wyposażonym w zestaw testowy Cambox, umożliwiający identyfikację usterek.
Wszystkie czynności naprawcze serwis wykonuje w oparciu o dokumentację dostępną w programie ESI Tronic K zawierającą dokładne instrukcje naprawcze. W instrukcjach „krok po kroku” są opisane kolejne etapy naprawy wraz z dokładnymi siłami docisku oraz momentami dokręcania. Wspomniane siły oraz momenty dokręcania są jednymi z najważniejszych informacji przy precyzyjnej naprawie pompowtryskiwaczy UIP, szczególnie nakrętki cewki.
Naprawę pompowtryskiwacza w obszarze elektrozaworu rozpoczyna się od zamocowania pompowtryskiwacza w przeznaczonym do tego uchwycie umieszczonym w specjalnym imadle posiadającym śrubę dociskową (Rys. 6). Następnie wykonuje się demontaż, mycie i weryfikację poszczególnych części. Jeżeli stwierdzamy, że iglica i gniazdo są sprawne, przechodzimy do wykonania kilku czynności pomiarowych umożliwiających dobranie właściwych elementów regulacyjnych, których wymiana pozwala na uzyskanie prawidłowego skoku i nacisku sprężyny cofającej iglicę.
Pomiarów dokonuje się przy użyciu precyzyjnego cyfrowego czujnika pomiarowego wyposażonego w odpowiednie adaptery dostosowane do pomiaru danej wielkości (Rys. 7). Następnie wykonuje się obliczenia precyzyjnej podkładki regulującej. Za pomocą przyrządów pomiarowych oraz dodatkowych elementów montażowych możemy przystąpić do precyzyjnej regulacji skoku iglicy, a tym samym BIP-u.
Testowanie pompowtryskiwacza po naprawie.
Końcowym etapem naprawy jest wykonanie testu szczelności zmontowanego pompowtryskiwacza oraz testowanie na stanowisku EPS 815, podczas którego mierzymy dawki w kilku punktach obciążenia oraz rzeczywistą wartość BIP-u.
Naprawa przeprowadzona z użyciem właściwych części zamiennych oraz wyposażenia Bosch gwarantuje poprawną pracę silnika jeszcze przez wiele tysięcy kilometrów. Należy pamiętać, że przy kompleksowej naprawie należy zawsze wymieniać oryginalny zestaw końcówki wtrysku jeżeli przebieg pompowtryskiwacza wynosi ponad 200-250 tys. km.
Taką naprawę można przeprowadzić między innymi w serwisach należących do sieci Bosch Diesel Serwis i Bosch Diesel Centrum. Zachęcamy do naprawy.
Autorzy:
Zbigniew Pilewski
Maciej Kaczorowski
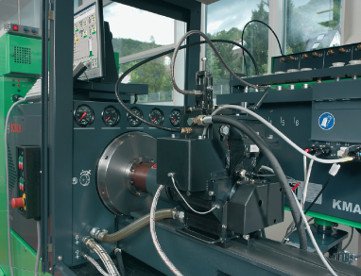
EPS 815: uniwersalne stanowisko testowe z wyposażeniem
Cam Box 847 do testowania pompowtryskiwaczy